

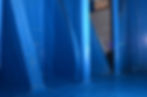

Internal Concrete Reservoir
Aquatan is able to successfully rehabilitate existing, and also line new concrete reservoirs. Our proprietary Ethylene Vinyl Acetate (EVA), based on its amorphous molecular structure, has the ability to accommodate an enormous amount of movement when compared to other similar products. Its superior flexibility, ability to be adhered, and ability to accommodate substantial movement makes it suitable for waterproofing of existing reservoirs.
It is known that existing reservoirs tend to crack due to differential settlement over the years of their service life. With Aquatan’s EVA geomembrane we can cost effectively give these old structures a new lease on life. This superior material, coupled with Aquatan’s vast experience in reservoir lining gives us the edge to which our clients have become accustomed.